Examine This Report on Sandblasting - An Overview - Sciencedirect Topics
Sandblasting a stone wall Diesel powered compressor utilized as an air supply for sandblasting Abrasive blasting, more commonly called sandblasting, is the operation of by force moving a stream of abrasive product versus a surface under high pressure to smooth a rough surface, rough up a smooth surface, shape a surface area or remove surface area impurities - Different types of sandblasting.
The very first abrasive blasting process was patented by Benjamin Chew Tilghman on 18 October 1870. There are numerous variations of the procedure, utilizing various media; some are extremely abrasive, whereas others are milder. The most abrasive are shot blasting (with metal shot) and sandblasting (with sand). Reasonably abrasive variations include glass bead blasting (with glass beads) and plastic media blasting (PMB) with ground-up plastic stock or walnut shells and corncobs.
Some Known Details About Understanding Abrasive Media Blasting Basic Finishing Guide
A mild variation is sodablasting (with baking soda). In addition, there are alternatives that are hardly abrasive or nonabrasive, such as ice blasting and dry-ice blasting. Sand blasting is likewise called abrasive blasting, which is a generic term for the procedure of smoothing, shaping and cleaning up a tough surface area by forcing solid particles across that surface at high speeds; the effect resembles that of using sandpaper, but supplies a more even complete with no problems at corners or crannies.
An artificial sandblasting process was patented by Benjamin Chew Tilghman on 18 October 1870. Sandblasting devices typically includes a chamber in which sand and air are blended. The mix travels through a hand-held nozzle to direct the particles towards the surface or work piece. Nozzles come in a variety of shapes, sizes, and products.
The Best Strategy To Use For Media Blasting Basics- 5 Tips To Make Your Blaster Work Better ...
Among the original pioneers of the damp abrasive (vapourmatting) procedure was Norman Ashworth who discovered the benefits of using a wet procedure a strong alternative to dry blasting. The procedure is offered in all traditional formats including hand cabinets, walk-in booths, automated production equipment and total loss portable blasting units.
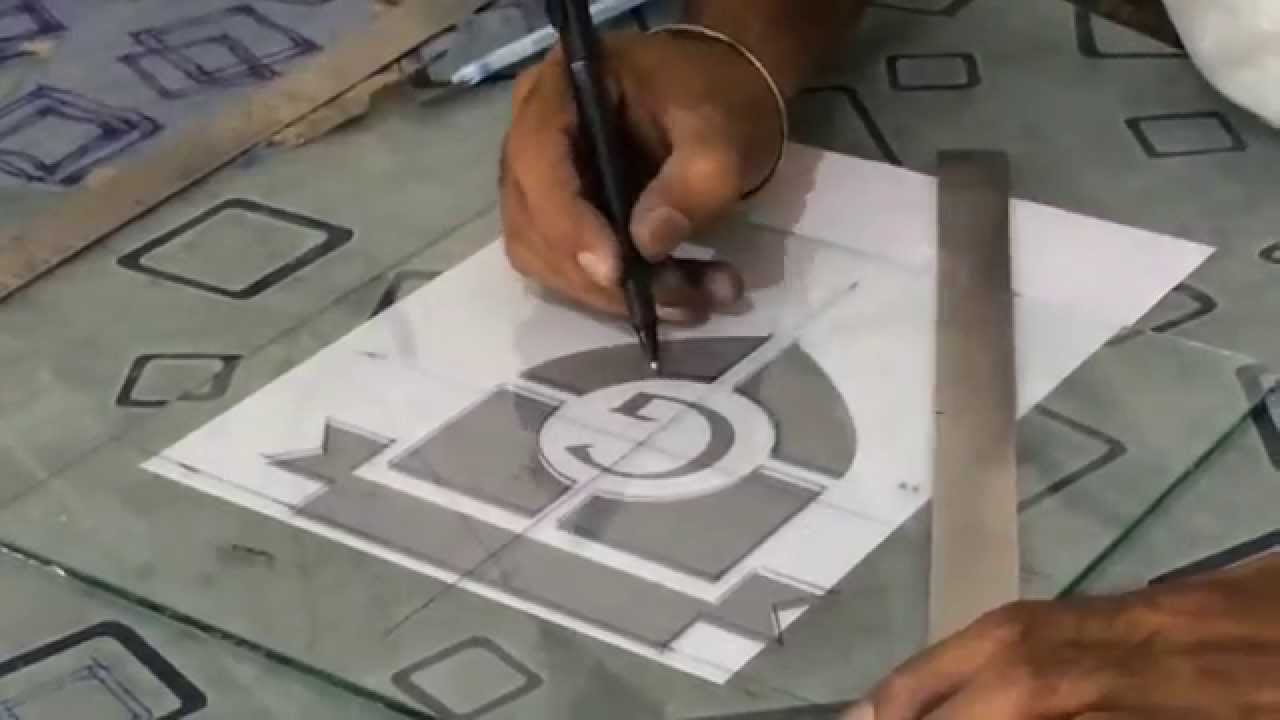
The reduction in dust also makes it much safer to utilize silicacious materials for blasting, or to get rid of harmful material such as asbestos, radioactive or dangerous products. Process speeds are typically not as fast as standard dry abrasive blasting when utilizing the equivalent size and kind of media, in part due to the fact that the existence of water between the media and the substrate being processed creates a lubricating cushion that can safeguard both the surface area and the media, reducing breakdown rates.
Not known Details About Sandblasting Concrete Surface- Process And Advantages ...
Nevertheless damp blasting of mild steel will lead to instant or 'flash' deterioration of the blasted steel substrate due to the existence of water. The lack of surface area recontamination likewise permits the use of single devices for numerous blasting operationse.g., stainless steel and mild steel items can be processed in the same equipment with the very same media without issues.
Mixing particles with water significantly reduces dust. Bead blasting is the procedure of removing surface deposits by using fine glass beads at a high pressure without damaging the surface area. It is used to clean calcium deposits from swimming pool tiles or any other surface areas, eliminate ingrained fungus, and brighten grout color.
The smart Trick of Benefits Of Using Abrasive Blasting Before Surface Coating ... That Nobody is Talking About
In getting rid of paint for vehicle body work, bead blasting is chosen over sand blasting, as sand blasting tends to produce a greater surface profile than bead blasting. Bead blasting is frequently used in developing an uniform surface area finish on machined parts. It is furthermore used in cleansing mineral specimens, the majority of which have a Mohs firmness of 7 or less and would therefore be harmed by sand.
It is typically categorized as an airless blasting operation since there is no propellant (gas or liquid) used - Sandblasting equipment. A wheel device is a high-power, high-efficiency blasting operation with recyclable abrasive (generally steel or stainless-steel shot, cut wire, grit, or likewise sized pellets). Specialized wheel blast machines propel plastic abrasive in a cryogenic chamber, and is usually utilized for deflashing plastic and rubber parts.
3 Easy Facts About How To Sandblast & How To Use A Sandblaster For Maximum ... Described
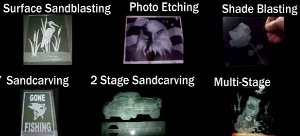
The first blast wheel was patented by Wheelabrator in 1932. In China, the very first blast wheel was developed around the 1950s, Qinggong Machinery is one of the earliest makers of blast wheel. Hydro blasting is not a type of abrasive blasting as no abrasive media is used. Hydro-blasting, commonly referred to as water blasting, is frequently used due to the fact that it generally requires only one operator.
This approach is perfect for cleaning up internal and external surfaces because the operator is normally able to send the stream of water into locations that are challenging to reach using other approaches. Another benefit of hydro-blasting is the capability to regain and reuse the water, minimizing waste and mitigating ecological effect.
Abrasive Blasting - Wikipedia Things To Know Before You Buy
Usually the area to be blasted is from about 1 mm2 to just a few cm2 at a lot of. Likewise referred to as pencil blasting, the great jet of abrasive is precise enough to compose straight on glass and fragile adequate to cut a pattern in an eggshell - Best way to clean your boat. The abrasive media particle sizes range from 10 micrometres approximately about 150 micrometres.
The most common micro-abrasive blasting systems are business bench-mounted units including a power supply and mixer, exhaust hood, nozzle, and gas supply. The nozzle can be hand-held or fixture installed for automated operation. Either the nozzle or part can be moved in automatic operation. Automated blasting is merely the automation of the abrasive blasting procedure.
The 25-Second Trick For Sandblasting Concrete Surface- Process And Advantages ...
Care is typically needed to isolate the blasting chamber from mechanical parts that might go through dust fouling. In this type of blasting, air and dry ice are utilized. Surface area pollutants are dislodged by the force of frozen co2 particles striking at high velocity, and by minor shrinking due to freezing which interferes with adhesion bonds.
Solidified carbon dioxide is a fairly soft material, so is less devastating to the underlying product than sandblasting. Bristle blasting, unlike other blasting methods, does not require a different blast medium. The surface is dealt with by a brush-like rotary tool made from dynamically tuned high-carbon steel wire bristles. Repeated contact with the sharp, turning bristle pointers outcomes in localized impact, rebound, and crater formation, which all at once cleans up and coarsens the surface.
Things about Sandblasting - An Overview - Sciencedirect Topics
Blast media usage is fairly low with this technique, as the used blast media is automatically separated from dust and loosened particles, and reused a number of times. Gadget utilized for including sand to the compressed air (top of which is a screen for including the sand) Mobile dry abrasive blast systems are typically powered by a diesel air compressor.
Blast pots are pressurized, tank-like containers, filled with abrasive material, utilized to permit an adjustable amount of blasting grit into the primary blasting line. The variety of blast pots is determined by the volume of air the compressor can provide. Totally geared up blast systems are often discovered installed on semi-tractor trailers, offering high movement and easy transport from site to site.
Our Media Blasting Basics- 5 Tips To Make Your Blaster Work Better ... Statements
In damp blasting, the abrasive is introduced into a pressurized stream of water or other liquid, developing a slurry. Wet blasting is often utilized in applications where the very little dust generation is preferred. Portable applications might or may not recycle the abrasive. A blast cabinet is basically a closed loop system that allows the operator to blast the part and recycle the abrasive.
click here